Fastpro
Fastpro, “the real screw store,” specializes in the sale of screws and fasteners. With a broad assortment of over 10,000 items and a constantly expanding range, efficient inventory management is crucial to the company’s success. To continue offering fast and reliable services, Fastpro decided to upgrade its Vertical Lift Modules.
Although Fastpro had been using three Kardex 250 NT Vertical Lift Modules since 2001 for their inventory management, it became clear that it was time for an upgrade. The existing systems had been reliable, but technological advancements and increased customer demands made it necessary for the company to modernize its equipment. Fastpro therefore contacted Relevator to sell their old machines while simultaneously investing in new used Vertical Lift Modules.
After consulting with Relevator, Fastpro decided to sell their three Kardex 250 NT Vertical Lift Modules and replace them with newer and more efficient solutions. Relevator managed the sale of the three Vertical Lift Modules, freeing up both space and capital for Fastpro to invest in new equipment.
To optimize their inventory management, Fastpro chose to invest in two used Kardex Megamat RS 350 vertical carousels as well as two new Kardex Shuttle XP 500 Vertical Lift Modules from Kardex Remstar. One advantage of this approach was that all units, whether used or new, were delivered and installed simultaneously by the same supplier.
This ensured that Fastpro could benefit from original service and support from Kardex Remstar, even for the used machines. By using a single supplier for the installation, Fastpro was able to easily access consistent and professional service for all their Vertical Lift Modules, contributing to an efficient and trouble-free setup.
The new installation has had a significant positive impact on Fastpro’s operations:
With the new equipment, Fastpro has been able to optimize their inventory management, leading to faster order picking and reduced lead times. The new systems offer higher storage capacity, enabling the handling of a broader range of items. By selling the old machines and investing in a combination of used and new systems, Fastpro has gained more capacity for their money. The choice of a mixed solution allowed them to stretch their budget further, thereby optimizing storage capacity and efficiency even more.
This case demonstrates how well-thought-out planning can bring long-term benefits to a company. By working with a single supplier for both the disposal of old machines and the purchase of new used ones, Fastpro has not only saved time but also simplified the process.
Additionally, the choice of used machines contributes to a more environmentally friendly solution by extending the lifespan of the equipment rather than simply scrapping the machines from 2001. This is a clear example of how environmental awareness and cost efficiency can create significant long-term benefits for the company.
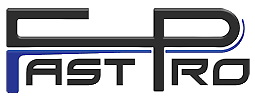