The ultimate guide about vertical carousels
Looking for information on vertical carousels? You’ve come to the right place!
At Relevator, we sell vertical carousels and other types of Vertical Storage Systems. Now, we’re sharing nearly ALL the knowledge we have about vertical carousels in this comprehensive and informative guide.
Find what you need directly through the table of contents or go through the guide to understand vertical carousels, as they are also known, in detail.
In this guide, we do our best to help you understand everything about how a vertical carousel works, why companies choose to use this technology, how a machine is constructed, and what to consider before a potential purchase – happy reading!
What is a vertical carousel?
Vertical carousels are a product within material handling and warehouse automation that uses the height of the machine type to store a large amount of goods in a small area. The principle is fundamentally based on the same construction as a Ferris wheel – storage trays rotating on a fixed frame/axis, like a carousel. For this reason, vertical carousels are sometimes also called paternosterverk.
The carriers in a vertical carousel rotate on arms, which keeps the stored goods always horizontal. Through the machine’s control panel, you can specify which carrier you want to pick goods from, and the tray then rotates to the machine’s opening where it’s easy to pick out goods and products.
The name “paternosterverk” is based on the Christian expression “Pater Noster,” meaning “Our Father” – a rosary with beads used in prayers. Later uses of the term “paternoster” included various types of dredgers (scoop wheels moving on an axis) or passenger elevators that functioned like carousels, known as paternoster lifts.
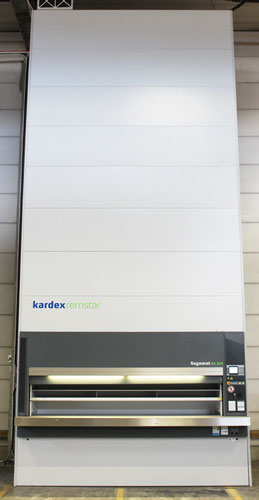
What manufacturers produce vertical carousels?
Vertical carousels are manufactured by both large and small players around the world. The most well-known global manufacturers are Kardex Remstar and Hänel, both based in Germany (Kardex also has its headquarters in Switzerland).
Worldwide the biggest players on the market are manufacturers such as:
- Jungheinrich
- Daifuku
- Linnex
- Vidir
- Alba
- Modula
- Kardex Remstar
- Hänel
- Weland Solutions
- SSI Schäfer
- and others
How is a vertical carousel constructed?
Before we delve into the advantages and specific applications of vertical carousels and warehouse carousels, we describe below how the machine itself is constructed. Fundamentally, the construction is relatively simple, which contributes to the robustness and reliability of the machine type. In simple terms, a machine consists of the following components:
- Side panels
- Base trays (Carriers)
- Cover plates
- Machine opening
- PLC/Control panel
- Motor
Side Panels
The side panels are the frame of a vertical carousel and constitute the machine’s fundamental structure. All other parts of a vertical carousel are mounted on these frames.
This component primarily determines two things: the height of the machine and the machine’s storage capacity.
Machine Height
The height of a vertical carousel is entirely determined by the height of the side panels. Unlike, for example, a vertical lift module, a vertical carousel cannot be adjusted in height; it is a fixed structure. For this reason, it is always important to try to find a height that matches your ceiling height as closely as possible when purchasing used equipment.
How is a vertical carousel constructed?
When purchasing a new vertical carousel, you can usually optimize this within an interval of 25-50 mm.
The maximum height of a vertical carousel is typically around 10 meters, depending on the manufacturer.
Machine Storage Capacity
There are more factors than just the machine’s side panels that determine a vertical carousel’s storage capacity, particularly the storage trays themselves – but the side panels are not insignificant.
In addition to the side panels coming in a specific height, they are also available in different depths. The depth of the side panels determines how deep the storage trays that can be mounted on the frame are – thus, in turn, the storage capacity in terms of both surface area (m²) and volume (m³).
The depth of the side panels usually ranges from 1,250 mm (narrowest variant) to 1,750 mm (deepest variant).
Another important aspect where the side panels affect the machine’s storage capacity is the thickness of the side panels. The thickness of the side panels is not something users typically need to consider, but for understanding the machine’s construction, it is adjusted according to how heavy the goods the machine needs to handle and how tall the machine is. A tall machine designed to handle heavy goods naturally requires somewhat thicker steel in its basic construction.
Carriers
The trays in a vertical carousel are often referred to in the industry as carriers. The configuration of carriers in a vertical carousel is a crucial factor in assessing the machine’s storage capacity in terms of both area, volume, and weight. A carrier’s capacity is based on 5 important properties:
- Carrier width
- Carrier depth
- Carrier height (pitch)
- Number of intermediate shelves
- Carrier maximum load
Carrier Width
When choosing a vertical carousel, the machine width, along with the machine height, is perhaps the most crucial dimension to consider. The machine width determines the width of the machine’s carriers and thus becomes a decisive component in achieving maximum storage capacity.
Carriers for a vertical carousel often come in standard sizes, and unless you make a special order, the approximate sizes listed below are what different manufacturers usually offer.
- 2,250 mm
- 2,450 mm
- 2,650 mm
- 2,850 mm
- 3,050 mm
- 3,450 mm
- 3,650 mm
- 4,000 mm
Carrier Depth
The depth of the carrier is naturally the second dimension that determines the vertical carousel’s storage capacity in terms of storage area (m², carrier width x carrier depth). The depth of a carrier is usually available in 3 different sizes with the following approximate measurements:
- 400 mm (370 mm – 420 mm depending on the manufacturer)
- 500 mm (470 mm – 520 mm depending on the manufacturer)
- 600 mm (620 mm – 640 mm depending on the manufacturer)
The depths are often tailored to work well with standard sizes of various types of storage bins.
Carrier Height (Pitch)
Carrier height is often referred to in the industry as “pitch”. Pitch is a very important dimension when selecting a vertical carousel as it determines the maximum height of the goods that can be stored in the machine. A carrier in a vertical carousel has fixed dimensions, and all the base trays in the machine move closely above/below each other.
Unlike a Vertical Lift Module that can automatically adjust to varying heights of goods, a vertical carousel has a maximum height based on the carrier pitch. Common carrier heights are, for example:
- 250 mm
- 300 mm
- 350 mm
- 400 mm
- 450 mm
- 500 mm
It is important to check whether the dimension provided by the supplier/manufacturer is the external dimension of the base tray or if it actually indicates the maximum storage height.
The pitch of a carrier determines how many base trays fit into the vertical carousel and how many intermediate trays each base tray can hold. A vertical carousel that is 8 meters high and has trays with a pitch of 250 mm can naturally hold more trays than if each base tray is 450 mm.
Number of Intermediate Trays
Another important component of a vertical carousel is what is called intermediate trays. Intermediate trays are simply additional trays that can be inserted into each carrier/base tray – an effective way to create more storage space and increase the number of storage locations in the vertical carousel.
A common configuration is, for example, that a carrier with a 350 mm pitch (height) can have 2 additional trays = this creates a carrier with 3 usable storage trays where each tray can accommodate a storage bin or goods with a maximum height of approximately 100+ mm.
Calculating Storage Capacity
Considering the above components (carrier width, carrier depth, carrier height/pitch, number of intermediate trays), you can calculate a vertical carousel’s capacity in both area (m²) and volume (m³). Below is a table with examples of common models. If you need assistance with similar calculations, feel free to contact us!
Model | Kardex Megamat RS 350.1.3250.5.381.31 | Constructor IPN8*2-520-341-4100/22-5490 | Hänel Rotomat 956 |
---|---|---|---|
Machine Height | 6 700 mm | 5 490 mm | 7 760 mm |
Machine Width | 3 875 mm | 4 800 mm | 3 420 mm |
Machine Depth | 1 571 mm | 1 700 mm | 1 670 mm |
Floor Space for the Machine | 6 m2 | 8,2 m2 | 5,7 m2 |
Carrier Width | 3 250 mm | 4 100 mm | 2 870 mm |
Carrier Depth | 528 mm | 520 mm | 640 mm |
Carrier Height / Pitch (Free Storage Height) | 350 mm | 340 mm | 450 mm |
Number of Carriers | 31 st | 22 st | 27 st |
Number of Intermediate shelves | 62 pcs, total 93 storage shelves | 22 pcs, total 44 storage shelves | 10 pcs, total 37 storage shelves |
Storage Area (m²) | 159,6 m2 | 93,8 m2 | 68 m2 |
Storage Volume (m³) | 18,6 m3 | 10,3 m3 | 22,1 m3 |
Carrier Maximum Load
The maximum load of a carrier is often determined by the motor power of the vertical carousel; however, the construction itself and the number of intermediate trays also play a significant role. Since intermediate trays have their own weight, a general rule is that the more intermediate trays a carrier has, the less load you can have in each carrier.
Common maximum loads for a carrier are often, for example, 300 kg, 400 kg, or 500 kg. As a general rule, a carrier that can handle a maximum load over 300 kg means that most operations don’t need to worry too much about overloading. However, if you handle relatively heavy goods, such as various steel parts, tools, etc., you should be cautious.
Below is an example of how the maximum weight of a Kardex vertical carousel is illustrated. Here, you can also see different types of intermediate trays:
- Self-supporting trays, which are slightly thicker and heavier but do not require support plates to stay upright.
- Simpler metal trays, lighter, which allows for higher load capacity, but requires support plates to prevent bending.
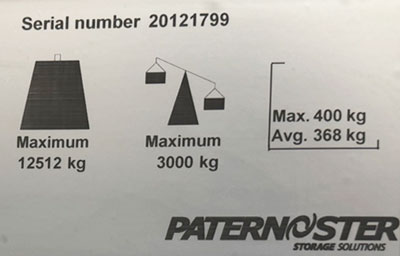
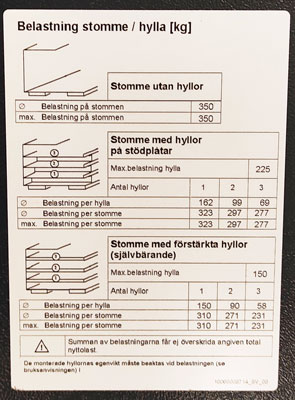
Cover Plates
When a vertical carousel has had its uprights erected and carriers installed, the construction is covered with plates, called cover plates. The primary function of cover plates is to enclose the machine to make it safe and aesthetically pleasing, but also to some extent to stabilize the construction.
When buying used vertical carousels, it’s worth checking that no cover plates are missing. When machines that were previously part of a pair or grouping are moved and placed individually, plates might be missing. While plates can be replaced, ordering them from the manufacturer can be relatively costly.
Machine Opening
The machine opening, or simply “opening,” in a vertical carousel plays a crucial role as it is where goods are both stored and retrieved from the machine. There are several important aspects regarding the machine opening:
Safety
The most critical safety system in the vertical carousel is located in the opening – the light curtain. The light curtain consists of laser sensors that run horizontally along the entire opening and ensure that neither goods, arms, hands, nor fingers can enter the shelves while the carousel is rotating.
If a finger or goods or a box falling suddenly breaks the light curtain, the vertical carousel stops immediately.
Opening Height
A common argument for storing goods in an automated storage system like a vertical carousel is that the operator/picker benefits from an ergonomic working position – this assumes that the machine’s opening is at a suitable height.
By default, the opening on a vertical carousel is approximately 1 meter above the floor.
When ordering a newly manufactured vertical carousel, it’s possible to customize the height of the opening. Customizing the machine’s opening often involves situations where the carousel is placed in a pit in the floor, requiring a higher opening, or for handling products with a specific forklift or material cart.
Work Surface
The work surfaces in the opening are horizontal platforms aligned with the opening that provide support and a workspace for handling products going in or out of the machine.
The work surface is usually 300 mm deep and made of some form of metal plate. When measuring a machine’s depth, the depth of the work surface is often excluded, so keep this in mind when considering a vertical carousel. For example, a machine with a depth of 1,600 mm often has a total depth of 1,900 mm including the work surface.
The work surface is very practical for both storing and picking, as you can extend it and let any storage bins that the carousel is filled with rest on the work surface while handling the goods.
Different surface finishes can be applied to the work surface if there are products sensitive to certain materials. For example, the work surface can be covered with a plastic/plexiglass layer if the products must not come into contact with other metals. Additionally, it is possible to install the vertical carousel without a work surface.
PLC/Control Panel
The PLC, or control panel, is the machine’s built-in “computer” that allows you to control the machine. Manual control of a vertical carousel usually involves entering the shelf level that you want to present at the machine’s opening.
The control panel also provides access to various settings and information about the machine, though this is typically not important for an ordinary operator.
The control panel is usually located above the machine’s opening, beside it, or in a separate enclosure, such as a data box or similar.
In some cases, the PLC/control panel may include additional system support features, such as the ability to hold item numbers and inventory levels. We rarely recommend using this functionality; it is more effective to place a regular PC beside the machine and continue managing inventory and other data in your WMS (Warehouse Management System). If you need more information about controlling and integrating automated storage systems and vertical carousels, you can read more here.
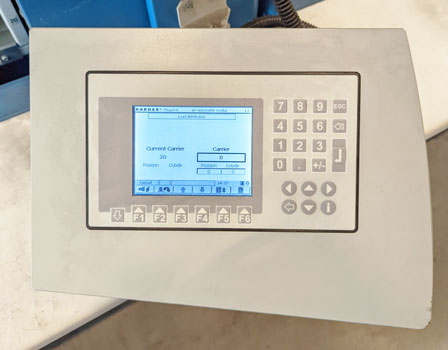
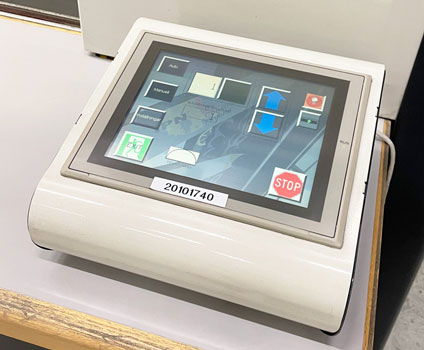
Motor
The motor of the vertical carousel can be crucial for determining the weight capacity of the machine. Besides allowing the handling of heavier loads, the motor model often dictates the robustness of the carousel’s other components, such as the thickness of the end panels and the maximum load capacity of the carriers (as described in previous sections).
For Kardex, motor models and capacities are described as follows:
- Kardex Megamat RS 180
- Kardex Megamat RS 350
- Kardex Megamat RS 650
Simplistically, the above models can handle 180 kg, 350 kg, and 650 kg per carrier/shelf, respectively. However, the maximum capacity of a vertical carousel is determined by more factors than just the motor.
Machine width, the number of intermediate shelves, machine height, and the motor can interact, and examples of how a machine’s capacity is illustrated on the vertical carousel can be seen below. Manufacturers usually have clear tables on their websites as well.
Optional Features for Vertical Carousels
In addition to the standard components of a vertical carousel, there are several optional features available, which often come pre-installed on used machines or can be customized when ordering a new machine. Below are some common solutions and options:
Machine Door
Adding a machine door to a vertical carousel is a very common solution. The machine door allows the opening of the carousel to be closed, either automatically or manually. The door helps to prevent dirt and dust from entering the machine when it is not in use.
A door on the vertical storage system can also be useful for securing valuable goods, thus reducing loss/theft.
LED Strip
An optional feature popular for increasing both the speed and safety of picking from a vertical carousel is the “LED strip”. The LED strip is a light bar embedded in the machine’s work surface at the opening, which uses LED lights and text to display information that simplifies and speeds up the operator’s work.
The most common use is to clearly indicate from which part of the shelf the goods should be picked. It is also common for the strip to display picking location, item description, and quantity to be picked, thus reducing the risk of picking errors.
ESD Design
If you work with products sensitive to static electricity, vertical carousels can be ordered with ESD (Electrostatic Discharge) protection. Components in the machine are replaced with ESD-protected alternatives, and most importantly, you can get ESD-protected bins and internal fittings for the vertical carousel.
Dual Openings
Another possible option for vertical carousels is to have dual openings, meaning two machine openings at different height levels. This can be a very practical feature if you want to utilize and use a vertical carousel on, for example, two different floors. An opening at floor level and one at a mezzanine level is a common application.
How to Choose the Right Vertical Carousel?
If you have decided to invest in one or more vertical carousels, there are, of course, numerous arguments for various configurations, models, and types. Below are our top tips.
Machine Dimensions
The most common and obvious consideration before purchasing a vertical carousel is the layout of your facility.
To maximize the utility of an automated storage system, you should always aim to utilize as much height as possible. The rule of thumb is that you can actually purchase a machine that is as close as 50 mm from your maximum ceiling height. Remember to measure from the lowest point of the ceiling, especially if you have sloped ceilings.
After height, width is the next major dimension to consider. The difference between a narrow and a wide vertical carousel can be as much as 1.75 meters—the storage capacity of a machine with 4,000 mm wide carriers is 70% higher compared to a machine with 2,250 mm width. If you have the space for it, our recommendation is to choose a as wide vertical carousel as possible.
Regarding the depth of a vertical carousel, the maximum difference in outer dimensions between a deep and a shallow machine is 500 mm. Carriers/shelves come in depths of 400 mm, 500 mm, and 600 mm—the maximum difference between a shallow and a deep machine is thus 50%. On the second-hand market, vertical carousels with 400 mm deep carriers are very rare, so if you find the right machine in height and width, don’t be overly concerned about this dimension.
Capacity
Storage Area
When choosing a vertical carousel, matching the capacity you need with the machine’s capacity is perhaps the most crucial factor to consider.
The most common scenario in a fully manual warehouse is having shelving units filled with storage bins. Shelving units are compact but usually don’t reach higher than 2 – 2.4 meters. A vertical carousel matches shelving units in compactness but utilizes ceiling height, thus saving a lot of floor space.
To make a rough calculation of your current utilization, you can calculate as follows:
- Number of rows of shelving units (e.g., 10)
- Number of shelving sections per row (e.g., 4)
- Number of shelves per section (e.g., 5)
- Size per shelf (e.g., 600 mm deep x 1,000 mm wide)
The above set of shelving units has a storage capacity in area according to the following calculation:
10 rows x 4 sections x 5 shelves x 0.6 m2 (600 mm x 1,000 mm) = 120 m2
This capacity is likely spread over an area of about 80 m2, according to the illustration below.
In comparison, you can refer to the table here. The calculation is the same but with the conditions of a vertical carousel:
How to Calculate Storage Capacity
To get an idea of the storage capacity of a vertical carousel, you can use the same calculation method as described previously. The conditions, however, differ for vertical carousels:
- Number of carriers (e.g., 31)
- Number of additional intermediate shelves (e.g., 62)
- Size per carrier (e.g., 528 mm x 3,250 mm)
The above vertical carousel has a storage capacity in area according to the following calculation:
93 shelves (carriers + intermediate shelves) x 1.716 m2 (528 mm x 3,250 mm) = 159.6 m2
These 160 m2 can be stored on only 6 m2 of floor space; the machine’s dimensions are 1.57 m x 3.88 m.
Storage Volume
Often, calculating the storage area is sufficient to get a good indication of the storage needs in a vertical carousel. Since vertical carousels are designed for relatively small products, the volume issue is often a minor concern; it’s mainly about creating many storage locations (sometimes thousands) in a small area.
If you want to calculate storage volume in more detail, you use the same calculation as above for storage area, with the addition of incorporating the height of each shelf into the equation.
An example scenario could look like this:
Shelving unit with 500 mm between shelves (2.5-meter high shelving unit):
10 rows x 4 sections x 5 shelves x 0.6 m2 (600 mm x 1,000 mm) x 0.5 m = 60 m3
Vertical carousel with a 350 mm pitch on the carrier:
93 shelves (carriers + intermediate shelves) x 1.716 m2 (528 mm x 3,250 mm) x 0.35 m = 55.85 m3.
As you can see from the example above, vertical carousels offer lower capacity in cubic meters compared to shelving units. The explanation here is that shelving units usually have a lot of air between the shelves, while a vertical carousel is often tightly packed.
Maximum Dimensions of Goods
When evaluating which vertical carousel to purchase, the maximum dimensions of your goods are important to consider. The most crucial factor is the height of the goods you plan to store. Vertical carousels are fantastic for storing small, compact products in a small area—however, if you have somewhat bulkier products, they may not fit in the carousel.
If you have products with heights of 300 mm, 400 mm, or even 500 mm, be extra careful to check the so-called “pitch” of the carrier/shelf. If the machine has a pitch of 350 mm, it simply will not be possible to store a product that is 400 mm high (unless it can be laid down or similar).
When it comes to the length and depth of your goods, the same principle applies: carefully check the dimensions of the carriers/shelves. It is unlikely that all goods and all types of dimensions will fit into one machine, but if you can accommodate a significant majority of your goods in the machine, the investment will usually prove worthwhile.
Weight
The maximum weight a vertical carousel can handle is also important to consider before purchasing. Generally, vertical carousels can be loaded with up to 300 kg, 400 kg, or 500+ kg per carrier/shelf, a capacity that works for most operations.
If you know that you have relatively heavy goods, the simplest way to check your needs is to measure a carrier or intermediate shelf on the floor or on a table. Then place the goods you intend to store on the marked area and weigh the products—did it exceed the carrier’s maximum capacity or not?
Number of Machines
Storage Capacity
If you are primarily looking for storage capacity, the evaluation is almost entirely based on the calculations you can see in the section above, regarding storage area and storage volume. Vertical carousels cannot be built indefinitely large, and often the height of a company’s facility is the major limitation.
Our example earlier was a vertical carousel at 6.7 meters in height with a total storage capacity of 160 m2. In a warehouse with a corresponding ceiling height of about 6.7 m, but where the storage need is 320 m2, you can simply calculate that you will need 2 machines.
Picking Efficiency
When it comes to picking efficiency, evaluating the number of machines needed becomes more complicated, but there are some guidelines.
First and foremost, if you aim to increase picking efficiency, you should always purchase 2 or more vertical carousels. One vertical carousel provides significant space savings, but using 2 or more, combined with a good WMS/business system, can achieve good figures in terms of picks per hour.
A well-designed picking strategy with 2 or more vertical carousels can mean that a warehouse worker can pick from 100 – 250 picking lines per hour, compared to a manual pick that typically ranges from 50 – 70 picking lines per hour.
A picking station for a warehouse worker optimized for efficiency usually contains 3-4 vertical carousels per picker—with such a setup, the picker never stands idle waiting for the machines and maintains a high picking pace at all times.
Choosing a Vertical Carousel Manufacturer
Companies that manufacture vertical carousels are all reputable players with good products, but the choice of supplier/manufacturer is still crucial.
Our main advice when evaluating the manufacturer is to focus on the complexity of your needs.
If you are buying 1 vertical carousel, which will be used sparingly and primarily for space-saving purposes, the manufacturer’s role will be relatively minor once the machine is installed. The products are very reliable, and there is seldom a need for support.
If you are buying 6 vertical carousels, storing a significant portion of your business’s inventory in them, and require extensive IT integration support, then it is important to thoroughly evaluate the manufacturer’s capabilities.
Here are some tips on what to investigate:
- What is the manufacturer’s delivery time for a machine?
- What is the delivery time for spare parts?
- How many service technicians does the supplier have locally?
- Is local telephone support available?
- Does the manufacturer have experience with similar solutions to what we are looking for?
- Are there any references we can call to hear about their experiences?
Summary
Investing hundreds of thousands (or millions) of kronor in a vertical carousel may seem like a big risk, but based on our experience, it is extremely rare to see customers and companies that do not benefit greatly from their vertical carousels.
This guide is quite comprehensive regarding useful information and decisions to make before purchasing a vertical carousel—but there are of course special cases and discussions to explore that are unique to your situation.
Whether you are interested in used products or need help evaluating the purchase of new vertical carousels, we are happy to assist you.
Feel free to contact us via the form, email, or phone!